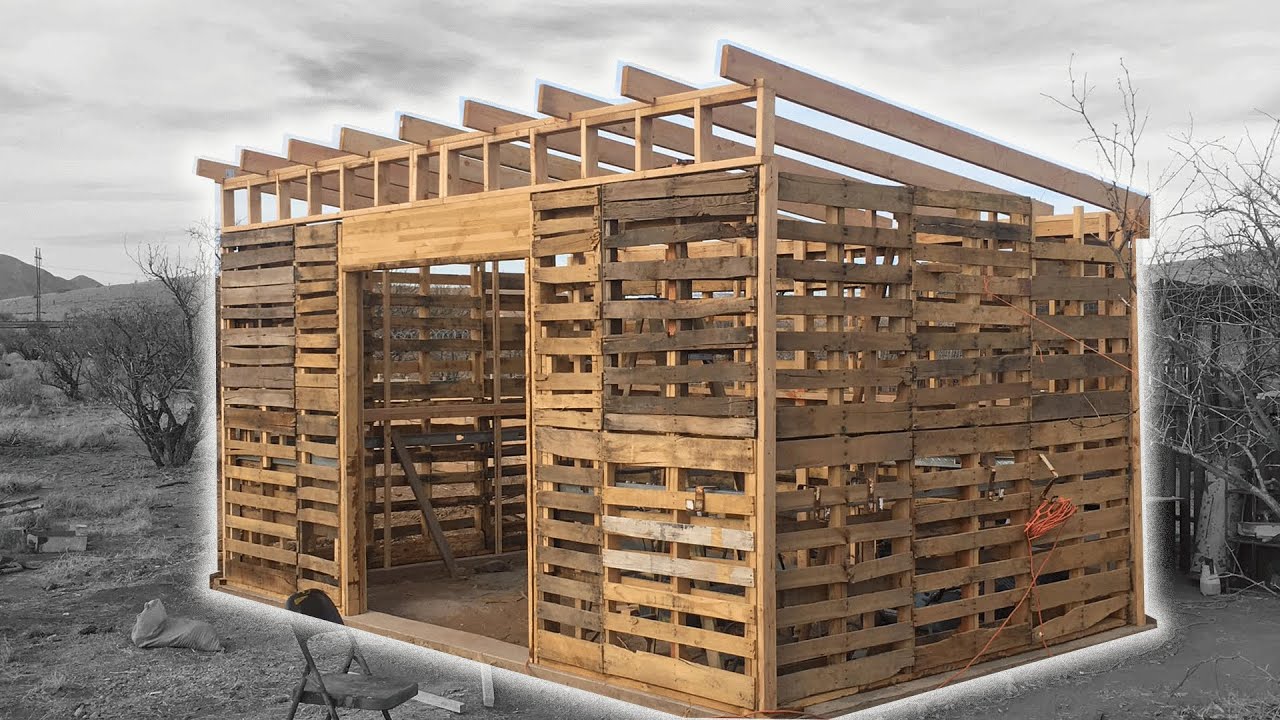
How to Build a Wood Pallet Shed: An Easy and Affordable DIY Project
Tired of overflowing garages and cluttered yards? Dreaming of a stylish, functional storage solution without breaking the bank? Then building your own wood pallet shed is the perfect project for you! This DIY endeavor offers a fantastic blend of affordability, sustainability, and personal satisfaction. By repurposing reclaimed wood pallets, you'll not only save money but also contribute to a greener planet. Let's dive into this exciting project and transform your outdoor space.
Planning Your Pallet Shed
Before you grab your hammer, careful planning ensures a smoother build. First, determine the desired dimensions of your shed. Consider the space available in your yard and the amount of storage you need. Sketch a simple plan, noting the placement of doors, windows (if desired), and any shelving. Next, source your pallets. Check with local businesses, construction sites, or even your own neighborhoodâ"many are happy to give away used pallets. Inspect them carefully; you'll need sturdy pallets free from rot, significant damage, or embedded nails. Finally, gather your tools and materials. You'll need basic carpentry tools (hammer, saw, screwdriver, level), screws or nails, possibly additional lumber for reinforcement, and any desired finishing materials like paint or sealant.
Essential Tools and Materials
To ensure a smooth building process, gather these essentials beforehand:
- Measuring tape and level
- Hammer and claw hammer
- Saw (circular saw or hand saw)
- Screwdriver (electric or manual)
- Safety glasses and work gloves
- Screws or nails (galvanized for outdoor use)
- Wood pallets (inspect for quality and structural integrity)
- Optional: Additional lumber for reinforcement or framing
- Optional: Paint, stain, or sealant for weather protection
Constructing the Pallet Shed Frame
Begin by creating the base of your shed. You can either build a simple platform using more pallets or create a more substantial foundation using concrete blocks or pressure-treated lumber. Once your base is secure, start assembling the walls. This involves strategically arranging and fastening the pallets together. For added stability, use screws or long nails and reinforce the corners with extra lumber. Remember to leave openings for doors and windows. Next, construct the roof frame. This could be a simple gabled roof or a flat roof, depending on your design and the available pallets. Again, reinforce the structure using additional lumber if necessary to create a strong and stable frame. Finally, attach the roof covering. Plywood, corrugated metal sheeting, or even more pallets can be used, depending on your budget and aesthetic preferences.
Finishing Touches and Considerations
Once the main structure is complete, it's time to add the finishing touches. Install the doors, ensuring they fit securely and swing smoothly. If you've included windows, install these as well. You might also want to consider adding shelving inside for better organization. To protect your shed from the elements, apply a weather-resistant sealant, paint, or stain. This will enhance the longevity of your shed and improve its appearance. Remember safety: always wear appropriate safety gear, such as safety glasses and gloves, throughout the construction process. Take your time and carefully consider each step before proceeding. Finally, step back and admire your handiwork! You've successfully built a functional and stylish wood pallet shed for a fraction of the cost of a commercially-made one.